
Manufacturingis the New IT

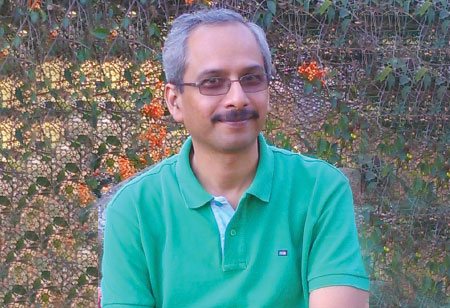
Dr. Sudhir Varadarajan, Dean - Design, Innovation, Incubation, IIITDM Kancheepuram, 0
Many leaders in the manufacturing industry are beginning to accept that Industry 4.0 is here to stay. Surveys organized by CII and other industry bodies show that while adoption of Industry 4.0 technologies is relatively low in Indian manufacturing when compared to countries like China, there is a high level of awareness today. This awareness is expected to drive increased investments and adoption of Industry 4.0 technologies in the next 5-7 years. Industry leaders believe that tech-savvy millennials are best suited to help the industry ride the wave of Industry 4.0. However, they are concerned that availability of young talent with the right competencies(blend of knowledge, skills and attributes) is a big challenge.
Manufacturing Needs Millennials
Some of the perceptions that have traditionally affected flow of young talent to manufacturing are that factory work means harsh working conditions, manufacturing is only for mechanical engineers, and salaries in the manufacturing sector may not be attractive. Naturally, engineers, especially women, tend to look for opportunities in the service sector like IT/IT-enabled services, financial services, retail and travel. Industry 4.0 is going to radically change this perception. Industry 4.0 involves leveraging Information & Communication Technologies, Industrial IoT, Data Science & Artificial Intelligence, and Augmented Reality/ Virtual Reality to digitalize the factory. The smart factory of tomorrow will be a very different place compared to the factories of today. This will open possibilities for young engineers, including women, to re-engage with manufacturing and contribute to this digital transformation in a big way. In other words, manufacturing is the new IT. However, it is imperative that young engineers develop three key competencies to be industry 4.0 ready.
Three Key Competencies for Industry 4.0
One of the key competencies that are required is the ability to reimagine operations. New technologies create possibilities for increasing productivity and reducing costs significantly, provided the teams can develop a deep understanding of the unique characteristics of the company’s operations i.e., product-process relationship, and challenge prevalent assumptions. Identifying the most compelling product service-process combinations, deciding the right level of intelligence, and picking the right metaphors & techniques will help increase the success of initiatives. For instance, manufacturers of
expensive and highly stressed components can use these technologies to track the impact of every manufacturing step on the component to minimize defects and penalties. In case of process industries like beverages, they can use these technologies to reduce unit cost through optimal use of energy at different stages of production.
The third competency required for Industry 4.0 is leadership. Young engineers need to develop an entrepreneurial mindset to spot business opportunities challenge prevalent assumptions, and collaborate with experienced professionals within & outside the company to develop & implement new solutions that deliver significantly higher productivity and cost savings.
Picking Academic Institutions that are Industry 4.0 Ready
Academic institutions are yet to gear-up to this challenge. The institute rankings or placement statistics do not necessarily capture the preparedness of an institute for the three key competencies for Industry 4.0. Even in cases where new programs have been launched, curriculum changes made or labs launched in partnership with platform vendors, the learning environments and pedagogy may not have fundamentally changed to support development of these new competencies.
It is important for prospective engineering students and their parents to look beyond the institute rankings and placement statistics. They need to pay attention to the finer details and everyday practices in institutions. For instance does the curriculum enable development of these key competencies in a systematic manner over the semesters; the percentage of credits given to inter-disciplinary subjects, softskills, practical work and industry internshipsy ratio for these types of courses the percentage of faculty with atleast five years of industry experience; and whether the credit system values the student’s learning effort or the faculty’s teaching effort. They should also try to get a glimpse of the everyday activities in the institutions by reaching-out to senior students.
Despite all the analysis about institutions, the admission process and competition may lead students to institutions that may be ill-prepared. Instead of cribbing about the institution, students must be prepared to take ownership for their learning. With this perspective, they will not only be able to navigate through the institution, but also contribute to it and develop leadership qualities. Above all, Industry 4.0 is a great opportunity for young engineers to contribute to national development and developing a new India. Millennials must use it and make a difference to the society.
The third competency required for Industry 4.0 is leadership. Young engineers need to develop an entrepreneurial mindset to spot business opportunities challenge prevalent assumptions, and collaborate with experienced professionals within & outside the company to develop & implement new solutions that deliver significantly higher productivity and cost savings.
Young engineers need to develop an entrepreneurial mindset to spot business opportunities, challenge prevalent assumptions, and collaborate with experienced professionals within & outside the company
Picking Academic Institutions that are Industry 4.0 Ready
Academic institutions are yet to gear-up to this challenge. The institute rankings or placement statistics do not necessarily capture the preparedness of an institute for the three key competencies for Industry 4.0. Even in cases where new programs have been launched, curriculum changes made or labs launched in partnership with platform vendors, the learning environments and pedagogy may not have fundamentally changed to support development of these new competencies.
It is important for prospective engineering students and their parents to look beyond the institute rankings and placement statistics. They need to pay attention to the finer details and everyday practices in institutions. For instance does the curriculum enable development of these key competencies in a systematic manner over the semesters; the percentage of credits given to inter-disciplinary subjects, softskills, practical work and industry internshipsy ratio for these types of courses the percentage of faculty with atleast five years of industry experience; and whether the credit system values the student’s learning effort or the faculty’s teaching effort. They should also try to get a glimpse of the everyday activities in the institutions by reaching-out to senior students.
Despite all the analysis about institutions, the admission process and competition may lead students to institutions that may be ill-prepared. Instead of cribbing about the institution, students must be prepared to take ownership for their learning. With this perspective, they will not only be able to navigate through the institution, but also contribute to it and develop leadership qualities. Above all, Industry 4.0 is a great opportunity for young engineers to contribute to national development and developing a new India. Millennials must use it and make a difference to the society.