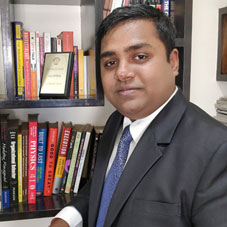
Parikshit Gupta
CEO
How has been the journey of Fastcomp so far and what makes it unique?
OHT Fastcomp was incepted in the year 1993 and from the beginning has been manufacturing hightensile fasteners, auto components, and technically critical engineering components, and providing heat treatment services. Our first heat treatment operation was for Godrej Boyce Mfg and over the years, have become one of the fastest-growing
companies in the industry. With a well-established setup, experienced management, a keen interest in research and development, and a constant willingness to accept new challenges, we have moved from strength to strength, maintaining quality and keeping cost and overheads in check.
Elaborate about the technology framework built within the company’s operations.
Our team has attended training programs on Forming Technology in Belgium which were conducted by Nedschroef Machinery which is a leading supplier of multistation, cold and warm metal forming machines. We have extensive knowledge of tool designing for manufacturing complicated parts leveraging which we have developed three machined parts in Cold Forging which save 25 to 30 percent material cost and increase its strength by 40 percent and switched to imported multi stations with a variable speed of up to 150 pcs/min. Moreover, we have modernized our Heat Treatment Furnaces and Forging machines which have saved 17 percent of electricity costs annually.
What value do you provide that cannot be replicated by anyone else in the market? Why do customers give you, their business?
For the past three years, we are with almost zero PPM with our customers. Our strengths & expertise lie in material science & failure analysis. We are a pioneer in the manufacturing of socket heads, flange, shoulder, and Torx bolts. We have a manufacturing capacity of 22 million bolts per month. We are financially strong, and our liability with our banks is extremely low. With the latest high-speed cold forming and thread rolling machine, we have the capability of developing cold forged components and are experts in resolving any hydrogen
OHT Fastcomp Is Envisioned To Become A World Class Company In Manufacturing Critical Components At The Customer’s Economical Rate
Elaborate about the technology framework built within the company’s operations.
Our team has attended training programs on Forming Technology in Belgium which were conducted by Nedschroef Machinery which is a leading supplier of multistation, cold and warm metal forming machines. We have extensive knowledge of tool designing for manufacturing complicated parts leveraging which we have developed three machined parts in Cold Forging which save 25 to 30 percent material cost and increase its strength by 40 percent and switched to imported multi stations with a variable speed of up to 150 pcs/min. Moreover, we have modernized our Heat Treatment Furnaces and Forging machines which have saved 17 percent of electricity costs annually.
What value do you provide that cannot be replicated by anyone else in the market? Why do customers give you, their business?
For the past three years, we are with almost zero PPM with our customers. Our strengths & expertise lie in material science & failure analysis. We are a pioneer in the manufacturing of socket heads, flange, shoulder, and Torx bolts. We have a manufacturing capacity of 22 million bolts per month. We are financially strong, and our liability with our banks is extremely low. With the latest high-speed cold forming and thread rolling machine, we have the capability of developing cold forged components and are experts in resolving any hydrogen
embrittlement problem. Furthermore, we have a record of achieving tightening torque of more than 35 percent of the standard; the achievement is due to our expertise in raw material selection and the control of heat treatment parameters.
Tell us about OHT Fastcomp’s approach toward Quality Management Systems. Talk about the different lab facilities of the company.
Our manufacturing facilities have an area of 300,000 sq. feet spread across two plants located in the state of Maharashtra. Both plants are equipped with state-of-the-art machines along with Scada based processes for quality control. We at OHT Fastcomp are geared with a customer oriented approach where each requirement is carefully considered and achieved ensuring quality and reliability. We have inbuilt Statistical Quality Control (SQC) systems at all our plants to ensure IS, ISO & DIN standards.
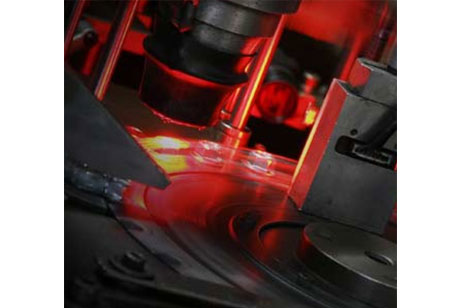
Our inhouse lab facilities include a Platting Thickness Measurement facility, Salt Spray Test Chamber, and Specimen Cutting & Polishing Machine. We have technologically advanced measuring equipment like Eddy current comparator, 1000x microscope, and Mitutoyo hardness & roughness testing machine. We also have a vision measuring machine along with CMM with Renishaw probe which is completely CNC based with a joystick to operate.
What is the role Fastcomp has envisioned to take shortly? And how is the team built to work towards the company’s vision?
OHT FASTCOMP is envisioned to become a world-class company in manufacturing critical components at the customer’s economical rate. Our mission is to be a vendor to all major compressor and automobile manufacturers by 2025. Our team is built on significant core values which are trust respect, integrity and customer centric services.
Tell us about OHT Fastcomp’s approach toward Quality Management Systems. Talk about the different lab facilities of the company.
Our manufacturing facilities have an area of 300,000 sq. feet spread across two plants located in the state of Maharashtra. Both plants are equipped with state-of-the-art machines along with Scada based processes for quality control. We at OHT Fastcomp are geared with a customer oriented approach where each requirement is carefully considered and achieved ensuring quality and reliability. We have inbuilt Statistical Quality Control (SQC) systems at all our plants to ensure IS, ISO & DIN standards.
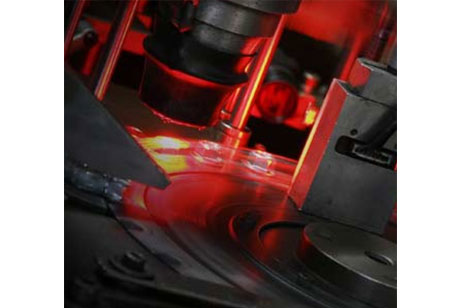
Our inhouse lab facilities include a Platting Thickness Measurement facility, Salt Spray Test Chamber, and Specimen Cutting & Polishing Machine. We have technologically advanced measuring equipment like Eddy current comparator, 1000x microscope, and Mitutoyo hardness & roughness testing machine. We also have a vision measuring machine along with CMM with Renishaw probe which is completely CNC based with a joystick to operate.
What is the role Fastcomp has envisioned to take shortly? And how is the team built to work towards the company’s vision?
OHT FASTCOMP is envisioned to become a world-class company in manufacturing critical components at the customer’s economical rate. Our mission is to be a vendor to all major compressor and automobile manufacturers by 2025. Our team is built on significant core values which are trust respect, integrity and customer centric services.