
The Semiconductor Shortage: What Caused The Supply Crunch? How Long Will IT Last?

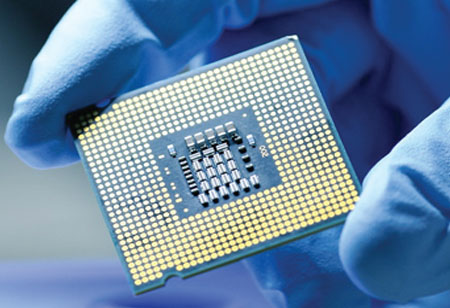
By Keerthana Kantharaj, 0
What began as a pandemic-era aberration of super charged demand for laptops and other chip-hungry gadgets has spiraled into a structural problem for the industry. Many chip executives say the problem will persist into 2023 and 2024, or even longer, as companies face equipment problems in manufacturing the chips. “There’s this wishful thinking that by the end of 2022, supply will be balanced with demand, I just don’t see it”, says Tom Caulfield, chief executive of contract chip manufacturer Global Foundries Inc. Even though there has been a shortage in the chip manufacturing worldwide semiconductor revenue increased 25.1 percent in 2021 to total $ 583.5 billion, crossing the $500 billion thresholds for the first time, according to preliminary results by Gartner.
How COVID Affected Chip Manufacturing Companies?
The coronavirus pandemic disrupted both supply and demand. On the supply side, many factories shut down, especially during the start of the pandemic. On the demand side, as remote work and studies became the norm, demand for laptops and other electronic devices surged. Once lockdowns were eased and the economy recovered, car sales, too, picked up. All this led to greater demand for chips. In late 2019, the Semiconductor Industry Association (SIA) projected an industry growth rate of 6.3 percent in value terms for 2021. It has since raised this to 25 percent, the highest growth in the last six years.
Ganesh Moorthy, CEO of Microchip Technology, a maker of microcontroller chips that process data in all kinds of electronic devices, including chipmaking equipment, says his company now is treating chip equipment suppliers as priority customers, not unlike the way it treated medical-device manufacturers at the onset of the COVID pandemic. Chip companies are pressing for such preferential treatment, arguing that if deliveries to semiconductor makers are given priority, the shortage will ease more quickly. A recent industry white paper argued the benefits of such a ‘multiplier effect’. A sophisticated testing tool requires 80 specialist chips that can be reprogrammed after they are produced, the analysis said, but then aids in making 320,000 of those same chips each year.
How is the Russia-Ukraine Crisis Protracting the Chip Shortage?
According to a report by Moody’s Analytics, palladium and neon are two resources that are key to the production of semiconductor chips. Now that Russia supplies over 40 percent of the world's palladium and Ukraine produces 70 percent of neon, we can expect the global chip shortage to worsen the military conflict persist. Taking lessons from the past events, the report noted that during the 2014-15 Crimea invasions, neon prices went up several times over, serving as an indication of the seriousness of the current crisis for the semiconductor industry.
How long will the Semiconductor Shortage Last?
The answer to that question is a function of two variables the existing stockpiles of these raw materials with chip manufacturers and the time for which the crisis in Ukraine prevails. Technology has improved significantly since 2015, and chipmaking companies have stockpiled resources owing to elevated demand during the pandemic, but inventory can only last so long. If a deal is not brokered in the coming months, expect the chip shortage to worsen and for industries highly dependent on them to be similarly affected.
This means significant risks are ahead for many automakers, electronic device manufacturers, phone makers, and many other sectors increasingly reliant on chips for their products to work”, Moody’s Analytics noted. According to a Reuters report, even as estimates on how many neon chipmakers have stockpiled vary widely, the consensus is that production could be hit if the conflict goes on. “If stockpiles are depleted by April and chipmakers don’t have orders locked up in other regions of the world, it likely means further constraints for the broader supply chain and inability to manufacture the end-product for many key customers”, CFRA analyst Angelo Zino was quoted as saying by Reuters.
Intel’s in House Model
Intel used to be the undisputed king of microprocessors. Many companies made PCs, but these were effectively just brand names. The prowess of the machines depended on whether they had an ‘Intel inside’. Here is how to compete as a chipset manufacturer: engrave more transistors on a slice of the silicon wafer. To achieve this, Intel outspent its rivals on R&D and attracted the best scientists. But most importantly, it kept full control of both product design and manufacturing.
Intel’s engineers from research to design to manufacturing have always worked as a close inhouse team. In contrast, fellow US rivals like Qualcomm, Nvidia,and AMD, have either shed their manufacturing capacity or never had it in the first place. They outsource to suppliers such as TSMC and other third-party foundries for the same reason, as most of the stuff sold in Wal-Mart is made in China: it is cheaper.The challenge with outsourcing manufacturing is that your suppliers are probably not in your building. Meetings will not happen at the water coolers or in the staff cafeteria. It takes scheduling and coordination.There is bureaucracy. It is hard to be on the same page.
According to a report by Moody’s Analytics, palladium and neon are two resources that are key to the production of semiconductor chips. Now that Russia supplies over 40 percent of the world's palladium and Ukraine produces 70 percent of neon, we can expect the global chip shortage to worsen the military conflict persist. Taking lessons from the past events, the report noted that during the 2014-15 Crimea invasions, neon prices went up several times over, serving as an indication of the seriousness of the current crisis for the semiconductor industry.
Chip Companies Are Pressing For Such Preferential Treatment, Arguing That If Deliveries To Semiconductor Makers Are Given Priority, The Shortage Will Ease More Quickly
How long will the Semiconductor Shortage Last?
The answer to that question is a function of two variables the existing stockpiles of these raw materials with chip manufacturers and the time for which the crisis in Ukraine prevails. Technology has improved significantly since 2015, and chipmaking companies have stockpiled resources owing to elevated demand during the pandemic, but inventory can only last so long. If a deal is not brokered in the coming months, expect the chip shortage to worsen and for industries highly dependent on them to be similarly affected.
This means significant risks are ahead for many automakers, electronic device manufacturers, phone makers, and many other sectors increasingly reliant on chips for their products to work”, Moody’s Analytics noted. According to a Reuters report, even as estimates on how many neon chipmakers have stockpiled vary widely, the consensus is that production could be hit if the conflict goes on. “If stockpiles are depleted by April and chipmakers don’t have orders locked up in other regions of the world, it likely means further constraints for the broader supply chain and inability to manufacture the end-product for many key customers”, CFRA analyst Angelo Zino was quoted as saying by Reuters.
Intel’s in House Model
Intel used to be the undisputed king of microprocessors. Many companies made PCs, but these were effectively just brand names. The prowess of the machines depended on whether they had an ‘Intel inside’. Here is how to compete as a chipset manufacturer: engrave more transistors on a slice of the silicon wafer. To achieve this, Intel outspent its rivals on R&D and attracted the best scientists. But most importantly, it kept full control of both product design and manufacturing.
Intel’s engineers from research to design to manufacturing have always worked as a close inhouse team. In contrast, fellow US rivals like Qualcomm, Nvidia,and AMD, have either shed their manufacturing capacity or never had it in the first place. They outsource to suppliers such as TSMC and other third-party foundries for the same reason, as most of the stuff sold in Wal-Mart is made in China: it is cheaper.The challenge with outsourcing manufacturing is that your suppliers are probably not in your building. Meetings will not happen at the water coolers or in the staff cafeteria. It takes scheduling and coordination.There is bureaucracy. It is hard to be on the same page.