
Implementing Industry 4.0 Principles in Textile Mills: Machinery and Beyond

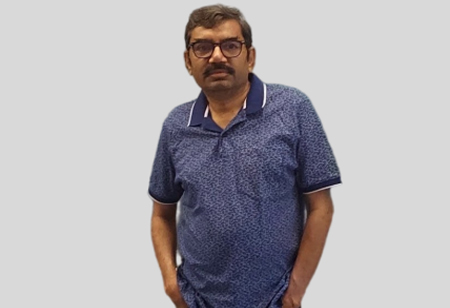
Shailendra Kumar Nigam, CEO, Mangal Textile Mills (India) Private Limited, 0
In an Interaction with Bimlesh Prasad, Correspondent at CEO Insights, Shailendra discusses his strategic textile manufacturing approach to cut operational cost and addresses the hurdles and prospects linked to the latest tech advancements and sustainability. He also explores the seamless adoption of advanced textile machinery to meet consumer demands. Below are the excerpts from the exclusive interview –
Tell us about the role of textile machinery in your strategic planning process, specifically for long-term development and growth?
As per Indian Economics, the textile sector contributes two percent to the GDP and around 14 percent to the manufacturing sector's GDP. The textile industry has changed a lot in the last few years. Now the use of AI and ML is needed for the future growth of the textile industry. Any sector depends on 3M—man, machine, and material. So out of three, 2M needs constant upgrades to improve efficiency of operation and profitability of business. Growth and development are linked to business sustainability. In this case, machine automation and detecting faults as early as possible during manufacturing are going to help. Machine automation is going to help reduce the utility cost of manufacturing, which is a main part of the operational cost. That’s why the machine selection process became an important activity for long-term business strategic planning. There was a time when, to reduce machine costs, a lot of mills purchased machines made in China. But now the focus is shifting again due to post-sale service and spare parts problems.
How has the advancement of textile machinery impacted the global textile industry's ability to meet increasing demand while maintaining quality standards?
Machines excel at rapid, precise, repetitive tasks, surpassing human abilities, propelling past industrial revolutions. Now, we must evolve manufacturing within 20 years—a new industrial era beckons. Artificial Intelligence (AI) and machine learning are pivotal in this transformation. In textile industry setup or upgrade, ROI reigns supreme to minimize manufacturing costs. Inefficient machines mean prolonged production and lower packing efficiency, squandering raw materials. Wastage offers no value. Take knitted fabric, where a broken needle may go unnoticed for meters. Enter scanners, introduced 15 years ago, but only stopping after damage below the knitting point, wasting 0.2 meters of fabric. Now, scanners must halt machines instantly upon needle breakage at the knitting point, salvaging fabric, boosting garment efficiency, and lowering costs.
Which technological innovations in textile machinery have had significant impact on reducing environmental footprint and promoting sustainability?
Energy cost and recycling of the textile are two major factors which will help on reducing environmental footprint and promoting sustainability. In this process I believe that sustainability of environmental is not only about nature, but also about all including business sustainability, environmental sustainability, employee
sustainability, Consumer sustainability. In the name of sustainability, sometimes we cross all limits and making products so costly that is going off range of consumer pocket. So, recycling textile waste is best way to sustain all. I believe as textile manufacture, we must give some tangible benefits to the consumer who helps to recycle the product.
What are the challenges and opportunities associated with retrofitting existing textile machinery to align with the latest technological advancements?
The primary challenge in this process for humans is ‘resisting change’, especially in the textile industry where machines and human labor are essential. While comfort zones are appealing, industrial growth necessitates embracing technological advancements and training the workforce for enhanced efficiency and profitability. Upgrading machines not only benefits the industry but also contributes to environmental conservation by reducing utility consumption.
Consider knitted fabric dyeing on soft flow machines as an example. Advancements in machine technology, compared to the 1990s and 2000s’ 70 liters per kilogram of water figure have dropped to 55–60 liters per kilogram in the 2000s–2010s. It further dropped to 45–50 liters per kilogram in the 2010s–2020s. Current technology has even achieved water-less dyeing using gas, underscoring the importance of machine upgrades.
This upgrade's environmental impact is twofold: reduced water consumption and decreased chemical usage, thereby alleviating the burden on effluent treatment plants. Some industrialists are opting to replace older machines with new technology, though this isn't always a straightforward choice. Machine suppliers often prefer selling entirely new machines, but some industrialists strike a win-win deal by acquiring a few new machines from the same supplier while allowing for possible modifications to existing ones. This approach benefits both parties involved.
How are industry leaders ensuring the seamless integration of advanced textile machinery to enhance quality control and meet consumer expectations?
Consumers need quality garments at affordable prices. As the growth rate of economics is slow, resultant textile item purchase became a need base rather than purchasing on change of fashion. So, it is the responsibility of Industry to reduce the cost of manufacturing by controlling wastage. In this process the quality control system is helping a lot. For example, in the stenter if we install the course counter as a quality control system it helps to maintain the consistency of fabric, resulting in better yield of garment. If we install temperature control system in the machine, then it will save the energy consumption to produce fabric, which will lead to sustainability of environment.
How do you envision the future landscape of the textile industry and its transformative impact on the entire value chain?
In 2023, an estimated 100 billion tons of garments will be produced, with nearly 92 million tons ending up in landfills. To grasp the scale, think of a trash truck filled with clothes dumped in landfills every second. Recycling waste in the textile industry is crucial, a practice rooted in Indian culture, now needed on an industrial scale.
Consider the past when a worn-out pant became a pillow cover, and later, a floor duster until it wore out completely. Today, with busy lives, such reuse is challenging. Yet, sending these garments to vendors who transform fabric into fiber for yarn and carpets offers a solution. Textile recycling, both pre and post-consumer, fosters environmental sustainability. Developing machines to convert textile waste into reusable materials is the future, promising reduced garment costs.
What are the challenges and opportunities associated with retrofitting existing textile machinery to align with the latest technological advancements?
The primary challenge in this process for humans is ‘resisting change’, especially in the textile industry where machines and human labor are essential. While comfort zones are appealing, industrial growth necessitates embracing technological advancements and training the workforce for enhanced efficiency and profitability. Upgrading machines not only benefits the industry but also contributes to environmental conservation by reducing utility consumption.
Consider knitted fabric dyeing on soft flow machines as an example. Advancements in machine technology, compared to the 1990s and 2000s’ 70 liters per kilogram of water figure have dropped to 55–60 liters per kilogram in the 2000s–2010s. It further dropped to 45–50 liters per kilogram in the 2010s–2020s. Current technology has even achieved water-less dyeing using gas, underscoring the importance of machine upgrades.
This upgrade's environmental impact is twofold: reduced water consumption and decreased chemical usage, thereby alleviating the burden on effluent treatment plants. Some industrialists are opting to replace older machines with new technology, though this isn't always a straightforward choice. Machine suppliers often prefer selling entirely new machines, but some industrialists strike a win-win deal by acquiring a few new machines from the same supplier while allowing for possible modifications to existing ones. This approach benefits both parties involved.
Upgrading machines not only benefits the industry but also contributes to environmental conservation by reducing utility consumption.
How are industry leaders ensuring the seamless integration of advanced textile machinery to enhance quality control and meet consumer expectations?
Consumers need quality garments at affordable prices. As the growth rate of economics is slow, resultant textile item purchase became a need base rather than purchasing on change of fashion. So, it is the responsibility of Industry to reduce the cost of manufacturing by controlling wastage. In this process the quality control system is helping a lot. For example, in the stenter if we install the course counter as a quality control system it helps to maintain the consistency of fabric, resulting in better yield of garment. If we install temperature control system in the machine, then it will save the energy consumption to produce fabric, which will lead to sustainability of environment.
How do you envision the future landscape of the textile industry and its transformative impact on the entire value chain?
In 2023, an estimated 100 billion tons of garments will be produced, with nearly 92 million tons ending up in landfills. To grasp the scale, think of a trash truck filled with clothes dumped in landfills every second. Recycling waste in the textile industry is crucial, a practice rooted in Indian culture, now needed on an industrial scale.
Consider the past when a worn-out pant became a pillow cover, and later, a floor duster until it wore out completely. Today, with busy lives, such reuse is challenging. Yet, sending these garments to vendors who transform fabric into fiber for yarn and carpets offers a solution. Textile recycling, both pre and post-consumer, fosters environmental sustainability. Developing machines to convert textile waste into reusable materials is the future, promising reduced garment costs.